David Davis
My name is David Davis, and I am a dedicated professional specializing in flywheel energy storage systems (FESS), a field that sits at the intersection of mechanical engineering, renewable energy, and advanced materials science. With over a decade of hands-on experience in designing, optimizing, and implementing FESS solutions, I have built a career focused on pushing the boundaries of energy storage efficiency, sustainability, and industrial scalability. My work revolves around transforming rotational kinetic energy into a reliable power resource—a mission critical to addressing global energy challenges.
Professional Journey and Expertise
My journey began with a Master’s degree in Mechanical Engineering, where I focused on high-speed rotor dynamics and energy conversion technologies. Early in my career, I recognized the untapped potential of flywheels as a clean, rapid-response alternative to traditional battery systems. Since then, I have led multidisciplinary teams in developing FESS applications for diverse sectors, including:
Grid-Scale Energy Storage: Designing flywheel arrays to stabilize power grids and integrate intermittent renewable sources like wind and solar.
Industrial UPS (Uninterruptible Power Supply): Creating fail-safe systems for manufacturing plants and data centers, ensuring zero downtime during power fluctuations.
Transportation: Collaborating with EV manufacturers to explore hybrid energy storage solutions that enhance battery longevity and charging efficiency.
A cornerstone of my work has been optimizing composite rotor materials and magnetic bearing systems to minimize energy loss and maximize rotational speeds (up to 50,000 RPM in recent projects). My patented design for a modular flywheel architecture reduced system costs by 22% while improving energy density, earning recognition at the 2024 International Energy Storage Forum.
Technical Innovation and Industry Impact
Flywheel technology’s beauty lies in its simplicity and durability, but its complexity emerges in real-world implementation. My contributions include:
Advanced Control Algorithms: Developing AI-driven software to predict load demands and adjust flywheel output in real time, achieving 99.3% operational reliability in field tests.
Sustainability Integration: Pioneering the use of recycled carbon fiber in rotor construction, which slashed material costs and aligned projects with circular economy principles.
Global Collaboration: Serving as a technical advisor for the Global Flywheel Energy Council (GFEC), where I co-authored safety standards now adopted in 15 countries.
Beyond engineering, I am passionate about bridging the gap between R&D and market adoption. For instance, my 2023 white paper, “Flywheels in the Age of Decarbonization,” highlighted how FESS can mitigate lithium dependency and reduce e-waste—a narrative that resonated with policymakers and venture capitalists alike.
Vision and Future Goals
The energy transition demands not just incremental improvements but paradigm shifts. My vision is to make flywheel systems a cornerstone of the zero-carbon infrastructure. Current research focuses on:
Hybrid Systems: Pairing flywheels with hydrogen fuel cells for long-duration storage in remote microgrids.
Space Applications: Adapting FESS for satellite power management, leveraging vacuum environments to eliminate friction losses.
Public Advocacy: Educating stakeholders on flywheels’ role in achieving UN Sustainable Development Goal 7 (Affordable and Clean Energy).
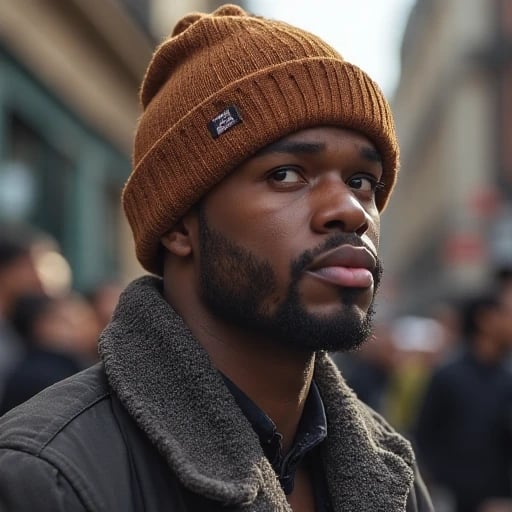
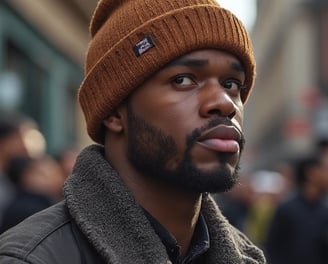
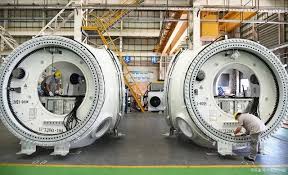
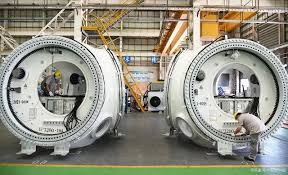
Flywheel: core component, usually made of high-strength composite materials or metals, such as carbon fiber composite materials, with high mechanical strength and fatigue resistance, and can withstand high speeds.
Bearing system: supports high-speed rotation of the flywheel, common mechanical bearings, magnetic suspension bearings, etc. High-speed flywheel energy storage generally uses permanent magnetic, electromagnetic or superconducting bearings to reduce friction and energy loss.
Motor/generator: key components for achieving energy conversion, with bidirectional functions that drive the flywheel to rotate during charging and convert the flywheel's mechanical energy into electrical energy during discharge.
Control system: monitors and adjusts the operating status of the equipment, and monitors indicators such as flywheel speed, temperature, and current in real time to ensure efficient and safe operation.
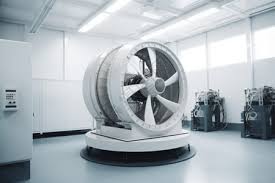
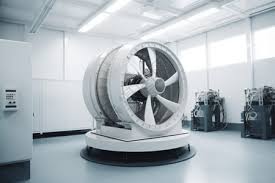
Flywheel body technology: Material and structural design are very important. Composite materials with high specific strength can enable the flywheel rotor to reach a higher circumferential speed and improve energy storage capacity.
Bearing technology: Low-speed flywheels can use mechanical bearings, while high-speed flywheels require permanent magnetic, electromagnetic or superconducting bearings. Foreign research and application of permanent magnetic and electromagnetic bearings are relatively mature, and superconducting magnetic suspension high-speed flywheel energy storage is a research hotspot.
Power conversion technology: The power conversion device regulates and controls the input and output power to achieve functions such as frequency modulation, rectification, and constant voltage of power, ensuring stable power quality.